4D Printed Polymers
Creators: Amy Ai, Victor Bienko, Kathryn Chen, Ryan Lee
Supervisor: Peter Yeadon
The studies that are featured below represent a series of explorations into the behavior of shape memory polymers, smart materials that are often referred to as 4D polymers because changes in temperature cause their three-dimensional form to change shape over time.
The CATALYST students first digitally modeled the shapes, and then printed the various forms using 4D polymer filaments. The activation temperature for the polymer is 60 ºC. Hot water was often used as a stimulus, so that the heat would evenly surround the material.
Amy Ai

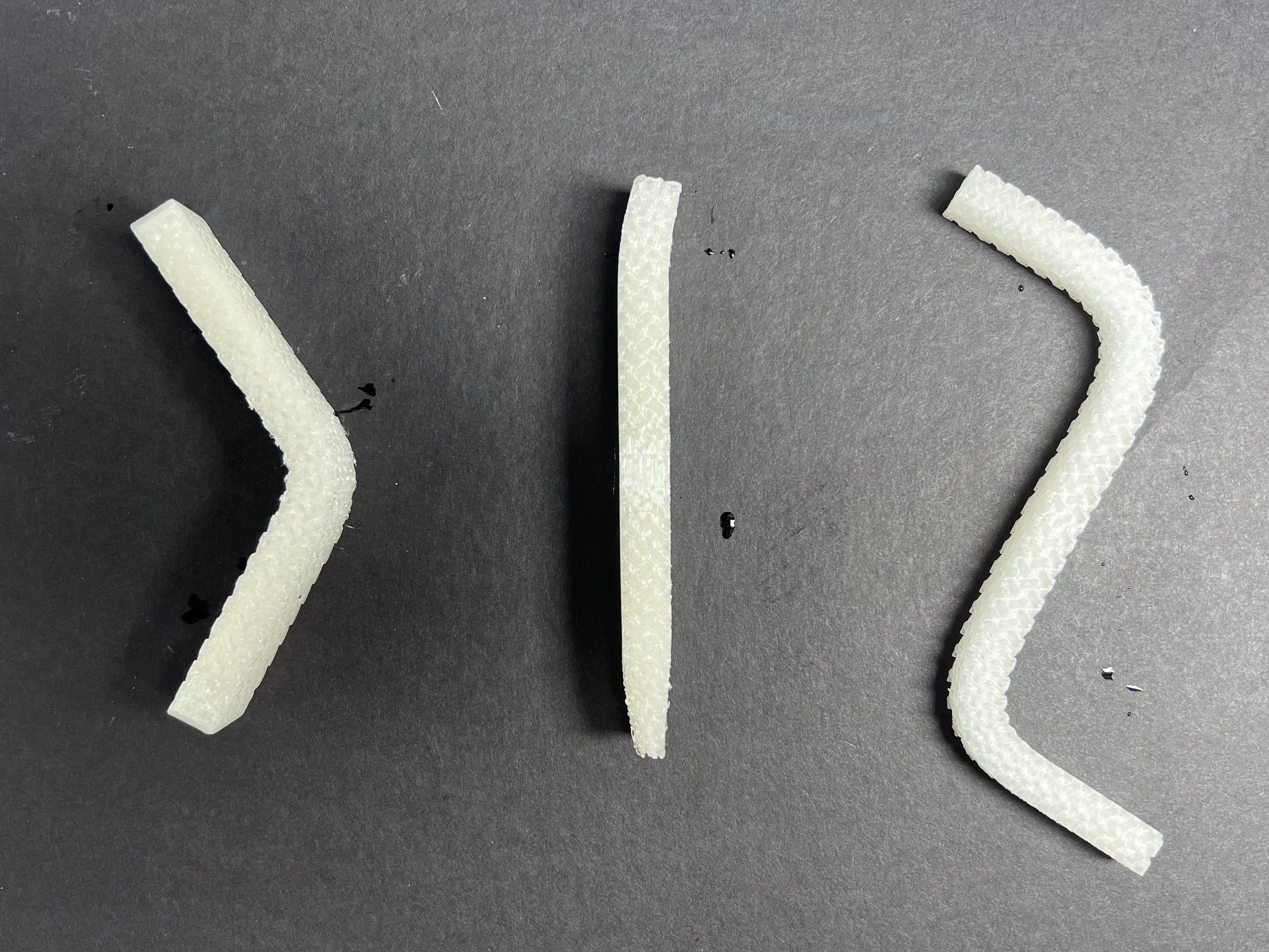

This series of experiments investigates how varying gyroid lattice densities influence the flexibility of shape memory polymers (SMPs). Here, flexibility is defined as requiring less force during bending, exhibiting a faster bending response, and having a shorter recovery time to the original shape under heat.
Two primary variables were tested: 1) cell size and 2) line thickness.
In the first experiment, three SMP samples (60mm × 10mm × 6mm) were 3D-printed with gyroid cell sizes ranging from 5mm to 10mm, increasing by increments of 2.5mm. Results indicated greater flexibility with larger cell sizes.
The second experiment assessed flexibility by altering line thickness within three SMP samples: variation one featured a central 1mm thickness transitioning to 2mm at the ends; variation two had a central 2mm thickness with 1mm ends; and variation three alternated thicknesses of 2mm and 1mm sequentially. Results indicated greater flexibility with thinner line thickness.
Findings demonstrated that manipulating cell size and line thickness in gyroid structures effectively programs flexibility and controlled bending behavior in materials of identical external dimensions.
Two primary variables were tested: 1) cell size and 2) line thickness.
In the first experiment, three SMP samples (60mm × 10mm × 6mm) were 3D-printed with gyroid cell sizes ranging from 5mm to 10mm, increasing by increments of 2.5mm. Results indicated greater flexibility with larger cell sizes.
The second experiment assessed flexibility by altering line thickness within three SMP samples: variation one featured a central 1mm thickness transitioning to 2mm at the ends; variation two had a central 2mm thickness with 1mm ends; and variation three alternated thicknesses of 2mm and 1mm sequentially. Results indicated greater flexibility with thinner line thickness.
Findings demonstrated that manipulating cell size and line thickness in gyroid structures effectively programs flexibility and controlled bending behavior in materials of identical external dimensions.
Victor Bienko
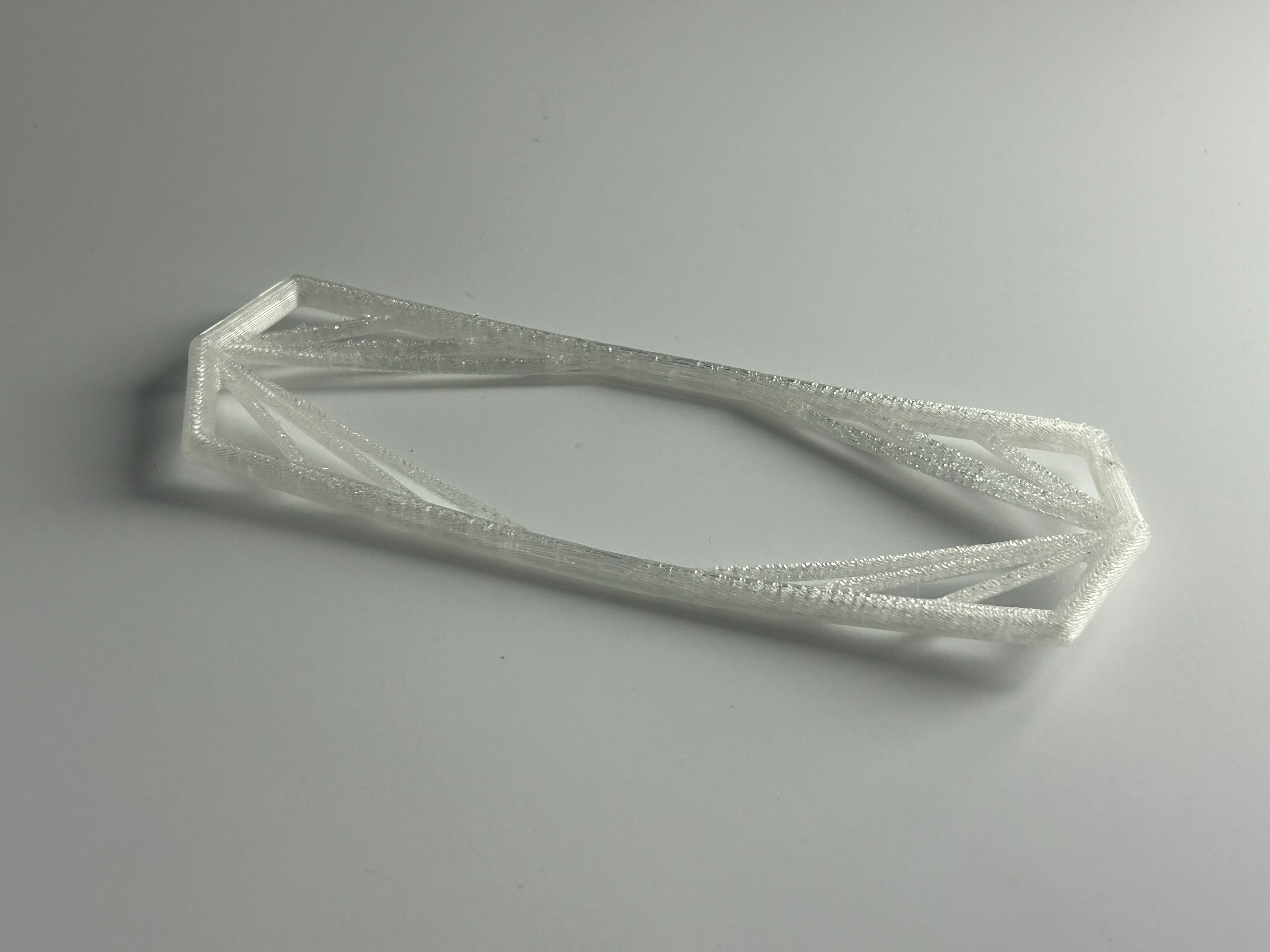

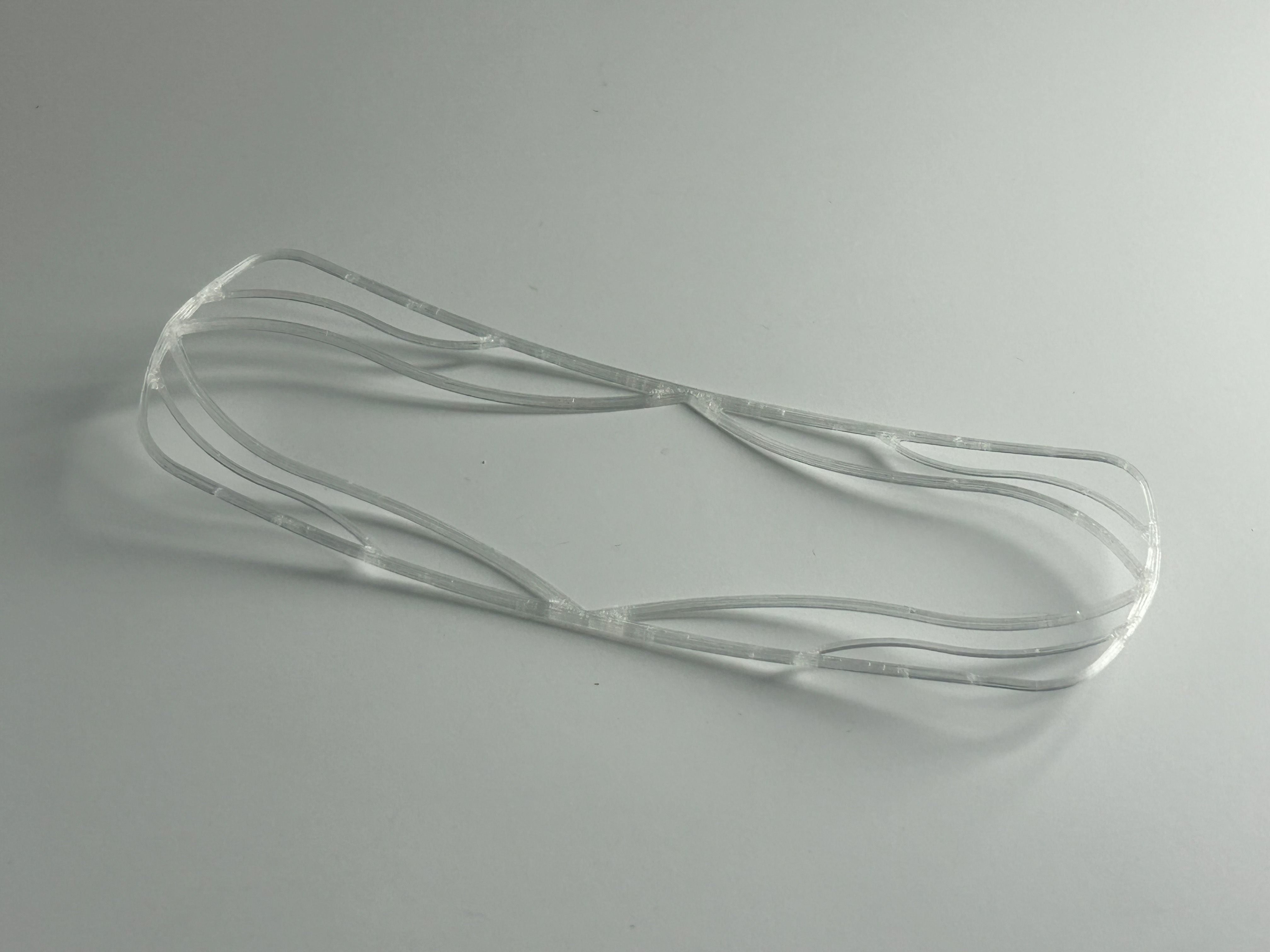
This exploration focused on making a board-shaped object out of shape memory polymer that could transform its sidecut radius, rocker/camber profile, and shape at extremities. This function was inspired by board sports such as snowboarding, skiing, and wakeboarding, for which equipment designs are forced to maintain shapes with advantages and disadvantages.
Initial explorations of the material clearly demonstrated that the material would not stretch along its grain or normal to its grain, but the direction and path of the grains themselves is very plastic and malleable when appropriately heated. The design of the board was changed from a solid mass to a framework of supports and holes that would lend itself best to deforming only in certain ways and about certain axes, keeping itself symmetrical and non-deformable at all other points and directions.
The location of supports and the overall shape of the frame were fine-tuned in pursuit of this objective. The final iteration was a very thin board-shaped frame that plastically deformed easily when heated and managed to be elastically compliant even when cooled.
Kathryn Chen
In this series of experiments, the goal was to explore the flexibility of volume in SMP (Shape Memory Polymer) 3D printed material. Vessels of varying thicknesses were printed, using wireframe-based structures for the experiments. The primary heating medium used in these tests was hot water, which allowed observation of the material's response to thermal stimuli. It was discovered that when the vessel walls are too thick, the material becomes difficult to manipulate, as it retains its form and resists deformation. In contrast, when the material is thinner, it becomes much more pliable, but also tends to revert quickly to its original shape once the heat is removed.
Additionally, another structure was created, featuring multiple small legs that can expand and stretch when heated. Following the same principle, it was observed that low-density, thinner material offers greater flexibility in terms of form change, as it responds more readily to the heating process. Future experiments include varying the density of these shapes to further examine how different material compositions impact their ability to transform and adapt to new forms, along with an examination of applied deformation forces.
Ryan Lee
This “thread-the-needle” experiment tests the ability of 3D-printed shape memory polymer (SMP) filament to return to its original looped “knot” configuration after being straightened into a line. It tests six different curve geometries which are constant in thickness but vary in terms of curve radius and length of material that passes beyond the loop.
The only successful curve that was able to re-loop itself was a curve with a smaller radius and a shorter length (Test 1B Trim). The common reason for failure was that the bend of the curve reformed from the middle to the end tip, preventing the end tip from passing through the loop as the bend became fully restored.
From this result, this study suspects that a curve with a smaller curve radius and a shorter length through the loop will have the highest likelihood of being able to re-loop itself.

Previous Next
Back︎︎︎