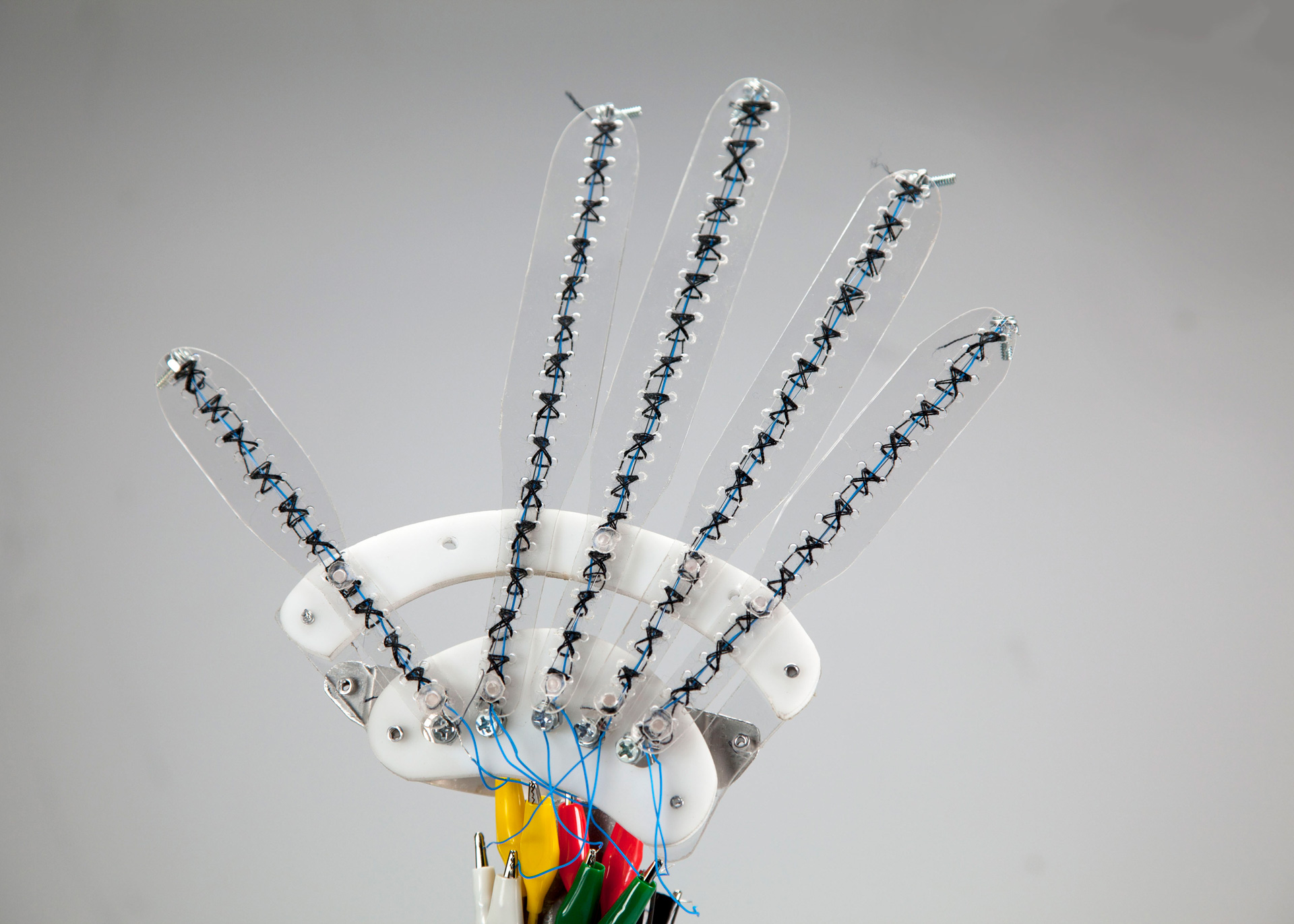
Astronaut Glove
Creator: Kaitlyn Schoeck
Supervisor: Peter Yeadon
This materials-driven study sought to discover a new application for smart materials that change shape when they are stimulated, with a focus on shape memory alloys (SMAs) that respond to changes in temperature. Many existing applications for SMAs focus on lightweight actuators, but this project resulted in a new kind of glove that helps astronauts overcome finger dexterity issues in Space, where weight isn’t necessarily a huge issue.
Current problems surrounding astronaut gloves include: lack of dexterity, muscle fatigue, loss of fingernails, discomfort, and injuries. Many complain that these bulky pressurized gloves are the first thing they want to have fixed. So scientists and designers have attempted to tackle this problem by reinventing the whole glove itself, with layers of various advanced materials, such as: Nomex, RTV Compounds, Teflon, and Aluminized Mylars.
Current problems surrounding astronaut gloves include: lack of dexterity, muscle fatigue, loss of fingernails, discomfort, and injuries. Many complain that these bulky pressurized gloves are the first thing they want to have fixed. So scientists and designers have attempted to tackle this problem by reinventing the whole glove itself, with layers of various advanced materials, such as: Nomex, RTV Compounds, Teflon, and Aluminized Mylars.
Researchers have also been testing bionic hands (myoelectric prosthetic hands), which tend to be heavy and require a lot of electronics in space. By fashioning artificial muscles out of lightweight shape memory alloy strands, and fully integrating these smart material actuators into each glove, Schoecke demonstrated a new approach to power-assist astronaut apparel.
The shape memory strands immediately contract with large, tunable forces when they are warmed. In the proof-of-concept prototype, the required temperature change is generated within the smart material itself, as it heats up in response to its resistance toward an electric current that’s introduced when needed. This enables the whole system to be controlled by suit systems.
The shape memory strands immediately contract with large, tunable forces when they are warmed. In the proof-of-concept prototype, the required temperature change is generated within the smart material itself, as it heats up in response to its resistance toward an electric current that’s introduced when needed. This enables the whole system to be controlled by suit systems.
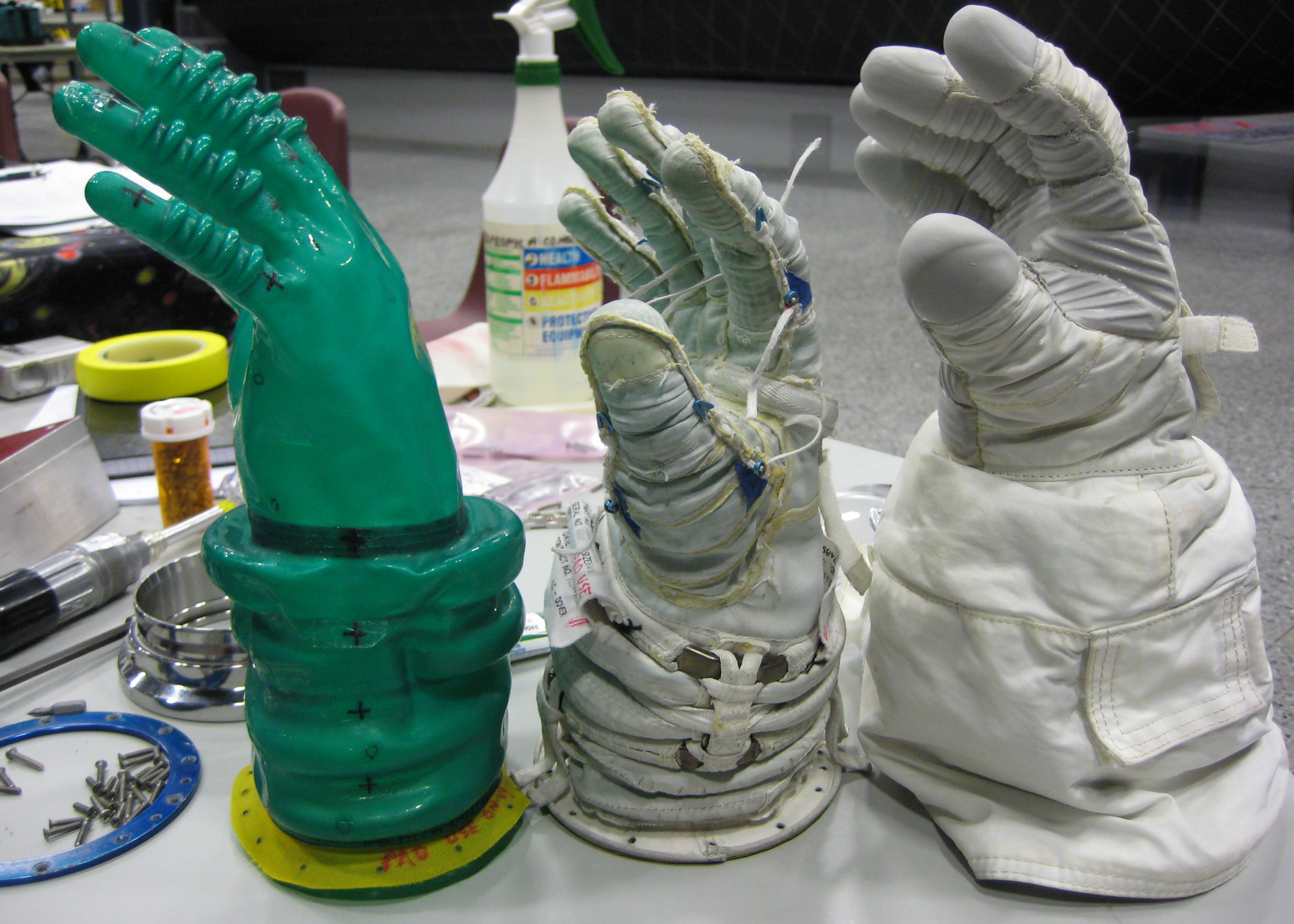
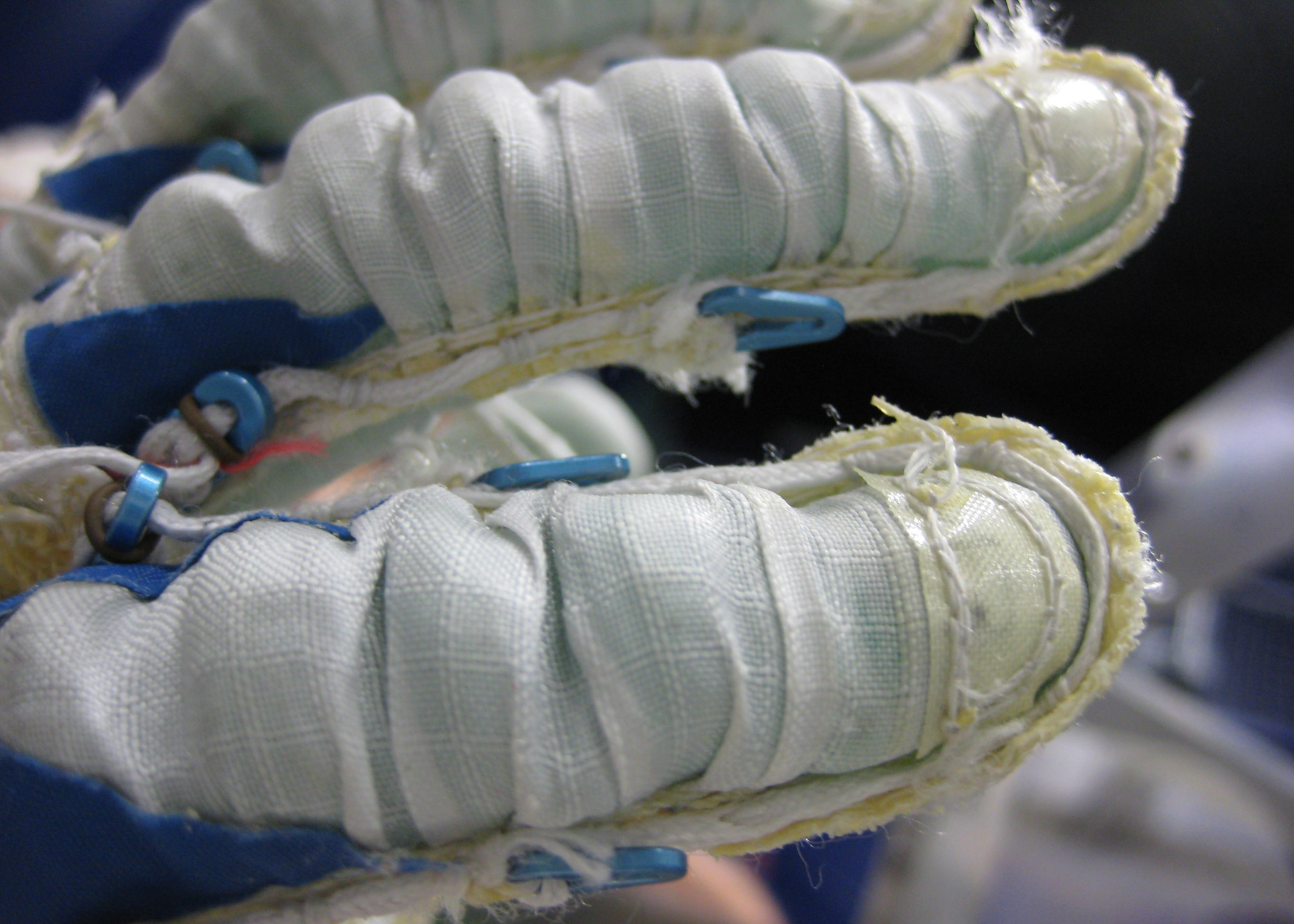
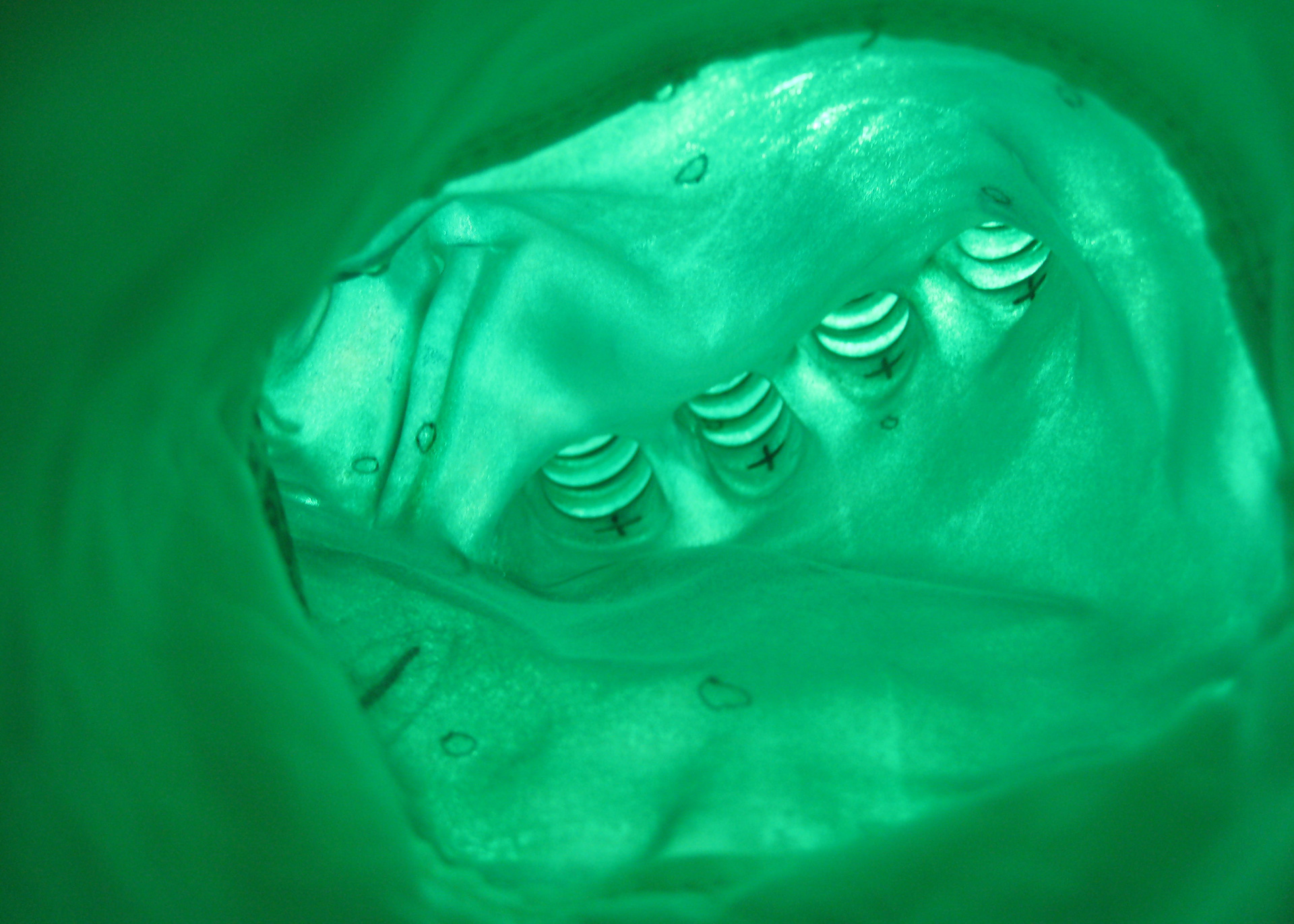

The SMA muscles would be integrated into the middle layers of the gloves. These layers can be composed of up to 8 material strata that include mylar, ripstop, and insulation. Within these layers, the Teflon-coated SMA wires would be threaded through on either side of each finger. Each finger of the glove would have pressure sensors that regulate current (and therefore heat) within the wires, as needed, so that the gloves can help each finger complete its desired movement and task.
Previous Next
Back︎︎︎